Coal Mines
During the 19th century a number of geologists suggested that coal might exist in the South East. A bed of lignite had been discovered in 1801 near Heathfield but this was of poor quality and was only sufficient to keep a local blacksmith going for two weeks. The existence of coalmines in France and Belgium suggested that coal might be found at a greater depth and boreholes were sunk at various locations in the hope of finding rich coal deposits. These were at Bexhill (1804), Rotherfield (1806), Maresfield (1806), Horsham (1813) and Mountfield (1872) but it was only at Dover that enough coal was found to make mining operations worthwhile.
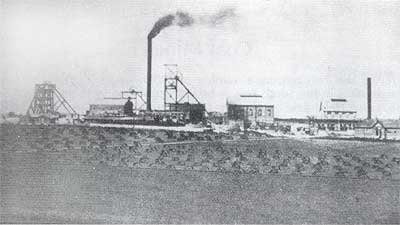
The Dover borehole was commenced in 1886 by the Kent Coalfields Syndicate Ltd on the site of the old Channel Tunnel works at Shakespeare Cliff, 3 miles west of Dover. It was stopped in 1893 at a depth of 2,230ft, having passed through 1,190ft of the Coal Measures and proved the existence of several coal seams. As a result of this, it was decided to sink a shaft down to mine the coal, especially a 4ft seam at a depth of 2,172ft. Shaft No. 1 (Brady Pit) was commenced near the borehole in July 1896. It was 17ft in diameter and rapidly passed through the Chalk, Chalk Marl and Gault Beds until it reached the Lower Greensand Beds in October at a depth of 366ft. At this point, so much water seeped into the shaft that it had to be abandoned.
The problem was that the Greensand Beds were pervious and contained a great amount of water which was held in position by the impervious Gault Beds above. As soon as the shaft pierced this cover, the water was released from pressure and was forced up the shaft. This is the principle of artesian wells and a similar effect can be obtained by placing an empty bucket into water and piercing a hole in the bottom — water will be forced into the bucket from below until it reaches the level of the surrounding water. Since the Greensand Beds here are at an angle, the level of the 'surrounding water' will correspond to the highest point that the Beds rise to in the area. This happens to be under the English Channel and so the Greensand will never run dry! In this case, water rose to within 40ft of the top of the shaft as it also had in the borehole.
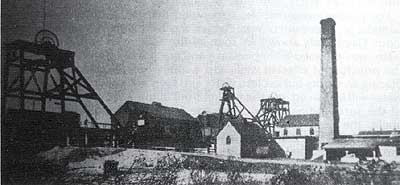
Shortly after Shaft No. 2 (Simpson Pit) was started nearby and was slightly wider at 20ft diameter. Having experienced water problems with the first shaft, the precaution was taken of putting down 15ft boreholes from the shaft bottom as it was sunk in order to give advance warning of flooding. At 10.55pm on 6th March 1897, a team of 14 men were working in the shaft bottom when the top bed of the Lower Greensand was struck. Initially there was no sign of water and there was no indication of danger until a few minutes later, when it was found that the sand was wet. Suddenly, water shot up into the shaft from underneath and only 6 men were able to escape by climbing up the iron rings supporting the timber lining. The hoppit (large bucket) was at the surface being emptied when cries were heard from below. It could only hold 3 men at a time and was quickly lowered twice to rescue survivors clinging to the shaft walls. Two men went down in the hoppit a third time but the water had risen 80ft up the shaft and they could see no more survivors. It took over a month before workers were able to pump out the shaft and recover the 8 bodies and work was suspended. It was subsequently found that the water level in the borehole and Brady Pit had dropped 127ft at the time of the accident. The probable explanation is that, under a head of about 265ft of water from both the nearby borehole and Brady Pit, sufficient pressure was exerted on the water in the Lower Greensand to burst through the few feet of hard sandstone and clay that formed the bottom of the shaft.
Despite this disaster, sinking later continued but Dover Colliery earned a reputation for costing a lot of money with little result. It was not until 1912 that the first (and only) consignment of coal was sent from the mine and this was only 120 tons! There was a big celebration to commemorate this but there were strong rumours that the coal had actually been brought from elsewhere to impress disillusioned shareholders. Needless to say, the colliery did not last much longer although iron ore was extracted for a short time.
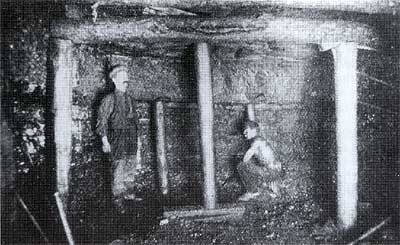
The turn of the century saw an enormous amount of activity in East Kent and over 40 boreholes were sunk to discover reserves of coal. Unfortunately for the reputation of the coalfield, a great many companies were set up of dubious intention and many shareholders lost money in speculative ventures. The kingpin at that time was Arthur Burr and he was associated with over 20 separate companies, many of which went into liquidation. His speciality was to be elected 'manager for life' of these companies and he transferred money between them as if they were all one (which effectively they were!). It seems amazing that he continued to persuade shareholders to invest in his schemes but people seemed hypnotised by the prospect of great profits to be made. When Burr was eventually make bankrupt, the judge made several scathing comments about his activities and called him a rogue. By squiring the mineral rights to most of the coalfield, Burr's companies effectively retarded development since they did not have enough capital to develop mines in a proper manner. The piecemeal development ended with nationalisation in 1947 when the National Coal Board took over.
In the event, the only collieries which were anything like productive were Betteshanger, Chislet, Snowdown and Tilmanstone. Others were sunk at Guilford, Stonehall and Wingham but these never produced coal. Before the bubble burst, there were grandiose schemes for many more collieries as well as complete new towns for the workers. The port of Richborough was intended to be the focal point of a lucrative export trade and plans were made for associated steel industries. Had these plans come to fruition, the countryside of East Kent would have been another South Wales or Lancashire. At the time of writing, the only working colliery left is at Betteshanger and its future is unknown. The usual policy of British Coal is to completely landscape coal mines when abandoned. As a result, few surface remains still exist and the Tilmanstone Colliery has been completely flattened. There are, however, still some remains of the private Guilford Colliery and the old engine house can be seen today in the farmyard which occupies the site.
Depth of Coal Mine Shafts
-
Betteshanger No. 12,162ft
Betteshanger No. 22,426ft
Chislet North1,470ft
Chislet South1,467ft
Dover 'X'520ft
Dover ‘Y’1,632ft
Dover 'Z’1,632ft
Guilford No. 1306ft
Guilford No. 21,272ft
Guilford No. 31,272ft
Snowdown No. 1262ft
Snowdown No. 23,083ft
Snowdown No. 32,994ft
Stonehall West273ft
Stonehall East273ft
Stonehall North75ft
Tilmanstone No. 11,590ft
Tilmanstone No. 23,168ft
Tilmanstone No. 33,139ft
Wingham East50ft
Wingham West150ft
There was another coal mine at Cobham near Rochester but this mined a poor quality brown lignite which outcropped at the surface in a small valley. For a number of years it had been opencasted by the landowner Lord Darnley who used it for domestic purposes at Cobham Hall. In 1947, however, an unlikely combination of a mining engineer, solicitor and cafe owner set up the Cobham (Kent) Mining Co. Ltd to mine it on a commercial scale. The mine was visited by the London Speleological Group who have left us with this record:
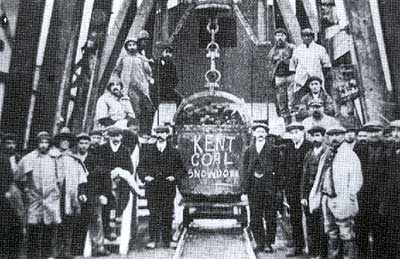
‘ . . . There are two drifts driven at right angles to the gulley. The West drift has been blocked by a fall but the other — the lifeline of the workings — is intact. This particular gallery extends for a distance of 55yds and has three working faces leading from it. The dip of the workings is 1:12 with a seam 6ft thick, no difficulty is experienced in working. At present, black lignite is being mined which resembles poor quality bituminous coal but some good bituminous coal has been found and larger strikes are expected soon. The overburden at the face is 60ft. Haulage is by tubs, one at a time, running on a single tramway and hauled by a diesel winch. Illumination is with acetylene lamps and all hewing is done by hand. Difficulty is being experienced with water which, besides flooding the workings, causes minor roof falls, made more likely by the fact that the roof is of shaly Woolwich and Reading Beds. However, the water is being kept under control with a petrol driven pump. With a working strength of 5 men, 3 at the face and 2 at the bank, the output per man per shift is 5.5 tons — 80 tons a week. The tonnage of ore available has yet to be proved but it is known that the seam extends 300yds to the East and a further seam of lignite is believed to exist 60ft below the present workings. It is proposed to drive an adit from the lower end of the gulley to the mine sump and so drain off the water. If the present labour force can be increased, an output of 150 tons a week is anticipated.'
This proposed expansion never happened since, as well as the water problems, the company was having difficulty in selling the product and encountered methane as the gallery was driven deeper into the hillside. It was eventually wound up in 1953 and the entrances were blown in. When the nearby A2 road was upgraded, the new carriageway passed over the site of the engine house and offices and little trace remains today. Opposite the Laughing Water Motel, about 100yds into the wood, a number of deep depressions exist which are the result of the collapsed workings.